General purpose motor drive - variating frequency and voltage
Control motor’s speed by variating the frequency and voltage of the motor signal in the power range from several hundred watt to megawatt
By varying the frequency and voltage of the motor signal, general-purpose drives enable the speed of a motor to be controlled. General-purpose drives are used in applications such as pumps and fans, process automation, or cranes in the power range from a few hundred watts to the megawatt range.
Our product offering combines excellent performance and reliability, offers a competitive price/performance ratio, and ensures the safety of your motor system. We offer you a broad portfolio of efficient semiconductors optimized for the motor inverter. Rely on our intelligent power modules (IPMs) and discretes for intelligent designs in the low power range. For medium power drives, our modules EasyPIM™ and EconoPIM™ are the perfect complements. For the high-performance range, EconoDUAL™ and PrimePACK™ are the solutions of choice. Combined with the innovative .XT interconnection technology, PrimePACK™ modules can help designers overcome the over-evaluation dilemma by extending lifetimes by increasing thermal and power cycle capabilities.
Highlights of our portfolio include our TRENCHSTOP™ IGBT7 modules, which are specifically designed to meet the requirements of drive applications. Ideal for general purpose drive (GPD) applications, TRENCHSTOP™ IGBT7 modules improve power density, controllability, and overload capability in a variety of proven packages to save cost and time. For high-speed drives and inverter integration, our CoolSiC™ MOSFETs are an attractive solution because they reduce switching and conduction losses, especially under partial load conditions.
In addition to our power semiconductors, we also offer gate driver ICs for all silicon and silicon carbide (SiC) devices. Our broad EiceDRIVER™ portfolio scales from basic to advanced functionality. The EiceDRIVER™ X3 Enhanced isolated gate driver portfolio now includes the X3 Analog 1ED34xx family and the X3 Digital 1ED38xx family with DESAT, Miller Clamp, soft-off, and I2C configurability. To complete this offering and get your design ready for Industry 4.0, we support the growing connectivity needs with XMC™ and the OPTIGA™ Trust solutions for the highest security standards. These devices can be combined with sensors from our XENSIV™ family to bring more sensory intelligence to your design and enable innovative features like predictive maintenance. Our range of external memory solutions enables advanced calculations for predictive maintenance.
In the technical introduction training, you became familiar with the full-bridge transformer driver family 2EP, which is a reliable power supply that supports Infineon’s top-notch switches and isolated gate drivers. By the end of this deep dive, you will be able to describe the working principle of this family and know about possible applications by understanding the effect of input voltage changes, transformer transfer ratio, and duty cycle changes on the isolated output voltage.
Leanr more about the 2EP EiceDRIVER™ power family, along with its features and advantages. Additionally, you will have an overview of the extensive application scope of the 2EP.
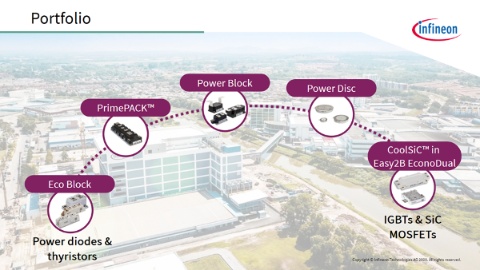
Do you want to know the various topologies you can find in this power conversion stage and their top-level working principle? Get to know the basic concepts of passive and two-level active rectification methods.
Tutorial about how to select reliable and efficient solutions regarding the requirements for industrial drives. We take a look on the key questions of power, voltage, topology, and frequency related to your application.
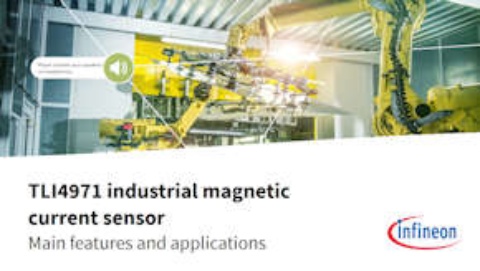
In this training you will:
- Understand the basics of the technology used by Infineon’s new TLI4971 current sensor
- Identify its main features, advantages and benefits