Servo motor drive and control
For applications ranging from several hundred watts to several hundred kilowatts
A servo drive is used to power electric servomechanisms by receiving a command signal from a control system, amplifying it, and transmitting the electric current to a servo motor. It allows producing motion that is proportional to the command signal. A servo drive monitors the mechanism's feedback signal. It also continually adjusts in case of deviation from the expected behavior. With this feedback, the commanded motion's accuracy can be ensured, and unwanted motion can be detected. A unique characteristic of the servo motor is that it consumes power while rotating to the desired position and then rests upon arrival.
Infineon offers you a broad portfolio of semiconductors for your servo motor design ranging from several hundred watts to several hundred-kilo watts applications. Our products are specially designed for use in Robotics, Material handling or machine tools, and many more to reach high reliability, longer lifecycle, high position accuracy, and fast response without overshoot.
Infineon offers you the tailor-made solution for your servo drives application with a wide variety of package types. In the lower power range up to 3 KW IPM, discrete and modules can be used. In this power range, silicon carbide MOSFETs offer optimal solutions for integrated drives. Alternatively, our IGBT7 technology is optimally designed for servo drives. With increasing motor power the share of modules for power semiconductors increases. Our Easy, Econo, EconoDUAL™3 and PrimePACK™ families offer customized solutions for every motor power class. If you aim a longer lifetime the PrimePACK™.XT portfolio is your choice.
For high-speed drives and inverter integration, our CoolSiC™ MOSFETs are an attractive solution because they reduce switching and conduction losses, especially under partial load conditions. Our broad EiceDRIVER™ portfolio scales from basic to advanced functionality. The EiceDRIVER™ X3 Enhanced isolated gate driver portfolio now includes the X3 Analog 1ED34xx family and the X3 Digital 1ED38xx family with DESAT, Miller Clamp, soft-off, and I2C configurability.
Servo drives require the highest standards of control accuracy. Our 32-bit XMC™ industrial microcontrollers based on Arm® Cortex®-M offer optimally matched solutions. For Industry 4.0 connectivity, we offer OPTIGA™ Trust security solutions. In addition, our high-performance memories for embedded systems offer high flexibility regarding the required memory performance.
SiC MOSFETs for servo drives
With more automation being used across industries, there is a correspondingly increased demand for servo motors. Their ability to combine precise motion control with high torque levels makes them the perfect fit for automation and robotics.
Using its manufacturing expertise and long experience, Infineon has developed a SiC trench technology that offers higher performance than the IGBT but with comparable robustness, e.g., short-circuit time of 2 µs or even 3 µs. Infineon's CoolSiC™ MOSFETs also address potential problems inherent in SiC devices, such as unwanted capacitive turn-on. Furthermore, the SiC MOSFETs are available in the industry-standard TO247-3 package, and now with even better switching performance, in the TO247- 4 package. Besides these TO-packages, the SiC MOSFET is also available in Easy 1B and Easy 2B packages.
The 1200 V CoolSiC™ MOSFET offers up to 80% lower switching losses than the corresponding IGBT alternative, with the additional advantage of the losses being independent of temperature.
As a result, a drive solution using CoolSiC™ MOSFET technology can achieve as much as a 50% reduction in losses (assuming similar dv/dt), based on lower recovery, turn-on, turn-off, and on-state losses. The CoolSiC™ MOSFET also has lower conduction losses than an IGBT, especially under light-load conditions.
In addition to the overall higher efficiency and lower losses, the higher switching frequencies enabled by SiC technology directly benefit both external and integrated servo drives in more dynamic control environments. It is possible due to the faster response of the motor current under changing motor load conditions.
This training talks about the integration of motors and drives with Infineon’s CoolSiC™ MOSFET and how this can help you overcome the limitations of traditional solutions.
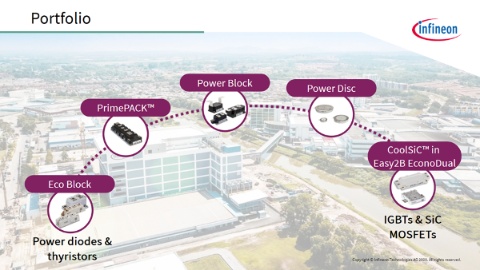
Do you want to know the various topologies you can find in this power conversion stage and their top-level working principle? Get to know the basic concepts of passive and two-level active rectification methods.
This training will introduce you to how the CoolSiC™ will help to design the next generation of servo drives.
Tutorial about how to select reliable and efficient solutions regarding the requirements for industrial drives. We take a look on the key questions of power, voltage, topology, and frequency related to your application.
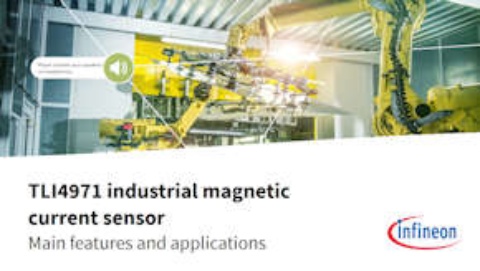
In this training you will:
- Understand the basics of the technology used by Infineon’s new TLI4971 current sensor
- Identify its main features, advantages, and benefits
Webinars
Servo drives come handy in a lot of applications, but controlling them and the power needed to drive them can be challenging when attempting to do it efficiently. Similarly, handling overload and short-circuit conditions is critical. Through this webinar, we will demonstrate best practices of protecting them and how to ensure the protection is reliable, robust and sufficiently fast for all operations. We will also give an exciting overview of suitable boards for evaluation and show the comprehensive Infineon portfolio of SiC MOSFETs and gate driver solutions.
Key Takeaways
- Understand how Infineon responds to the trends in the industry drives market: e.g. inverter integration with SiC MOSFETs and get an overview of some of the solutions offered
- Learn how to enable lower switching losses compare to IGBTs at same dV/dt levels and enhanced switching control
- Explore how to avoid the main pitfalls when driving SiC MOSFETs
- Discover how to reliably protect SiC MOSFETs using EiceDRIVER™ gate drivers