I am just really happy to have such a reliable employer. There will always be some things that could be better, but I really enjoy working for Infineon.
Maintenance Technicians
#WeAreIn to keep production running smoothly. Are you in?
Join us as Maintenance Technician.
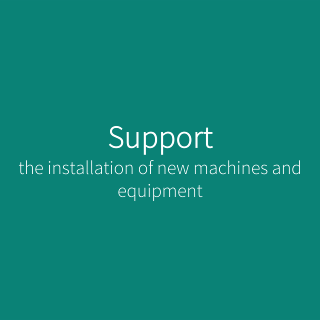
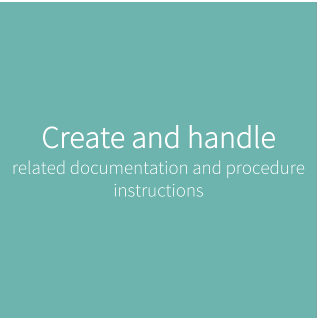
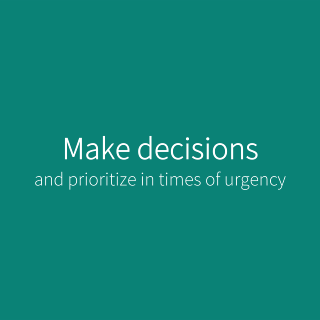
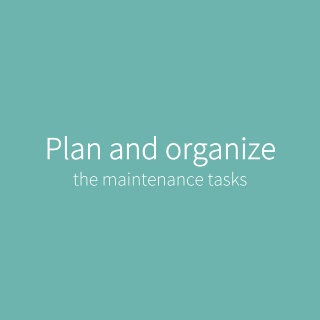
Have a look how our Maintenance Technician keep the production moving
Do you have any questions about these positions? Contact our career team.
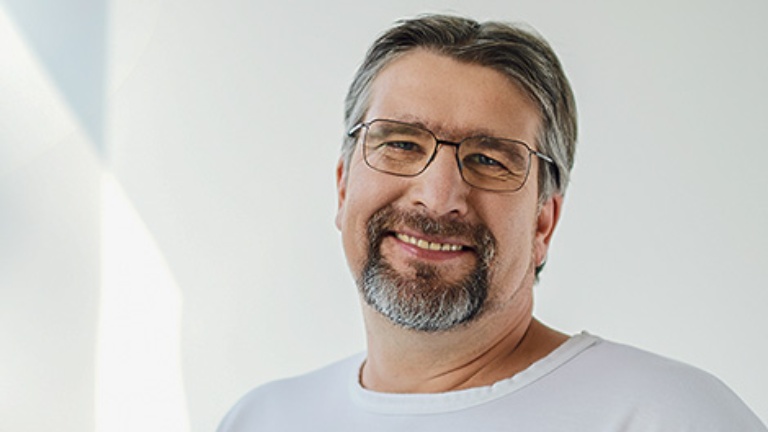
This is the perfect job for anyone who is intrigued by the complex interplay between the various components that make up a system.
Thomas' Story
Unraveling the complex interplay between different system components
Thomas started out as an operator (OP) with Infineon Dresden in 1998, moving on to the role of Maintenance Technician in 2020. His core tasks entail maintaining and repairing production systems, drawing on his problem-solving and analytical skills.
Thomas in five words:
ProblemSolver TechGeek Logician AnimalLover CommunicatorMaintaining and repairing wet chemical systems.
Well maintained machines run smoothly and that, in turn, translates into a high yield and – ultimately – profitable operations.
I enjoy the balance between the unpredictability of troubleshooting and the predictability of routine preventive maintenance. I love turning brain-teasers into moments of tangible success. Teamwork is also great, especially when we collaborate closely with the various specialists. It’s exciting to see everyone pull in the same direction to pinpoint a fault and get the machine up and running again. And to boot, you learn so much as a maintenance technician – and a lot of these insights are invaluable in your daily work.
Also you need a lot of in-depth knowledge to work quickly – but also meticulously. And it’s helpful to have the intuition and creativity that come with a problem-solving mindset. Ultimately, I really enjoy analyzing and solving failures.
With us, it’s all systems go as soon as a trouble report is filed or a machine fails unexpectedly. Every minute of downtime results in loss of yield and money. So our ultimate mission is to get the machines back up and running as quickly as possible – but not at the expense of long-term stability. We search for the exact fault in a methodical way and then quickly find a precise solution. And this often calls for a certain degree of creativity. For instance, if a part that is difficult to access needs to be replaced. There is no room for error with interventions such as these. The equipment is highly sensitive and the clock is ticking. Many things depend on the quality of my work. If one of the machines that I look after comes to a standstill, production in other areas also grinds to a halt. Good instincts and a steady hand are essential to locate the source of an issue. Equally important of course are expert insights, calm nerves, caution, and decisiveness.
Good and on time! As a team, we have to be able to rely on each other.
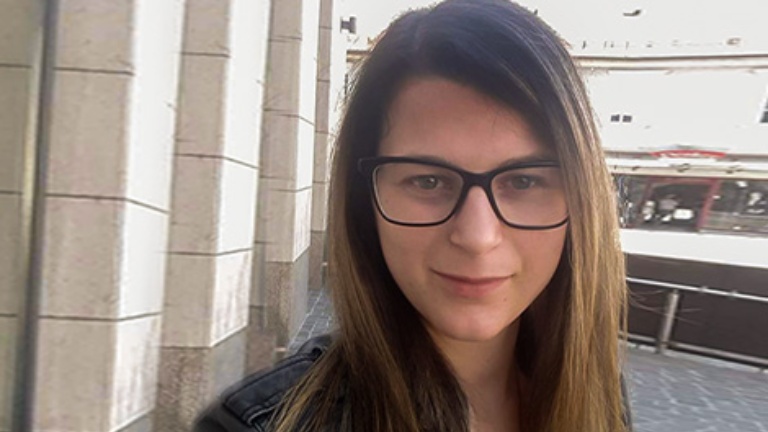
Every day in production feels like a new adventure! My job requires me to balance absolute precision with a sense of creativity; and an eye for detail with a clear view of the big picture. My team and I keep the wheels of production turning with our skills and expert knowledge.
Silke's Story
Keeping the wheels of production turning
Silke joined Infineon in Villach as an apprentice in 2012. Since 2016, she has been working as a Maintenance Technician in the plasma etch department. Her mission is to keep the wheels of production turning through a mixture of persistence and creativity.
Silke in five words:
CreativeThinker AnimalLover SolutionFinder TattooAddict AllrounderWorking at Infineon gives me a chance to help shape the future of microelectronics as part of an extremely innovative and international team.
Carrying out scheduled and unscheduled maintenance. Pinpointing and solving simple and complex faults in the production equipment.
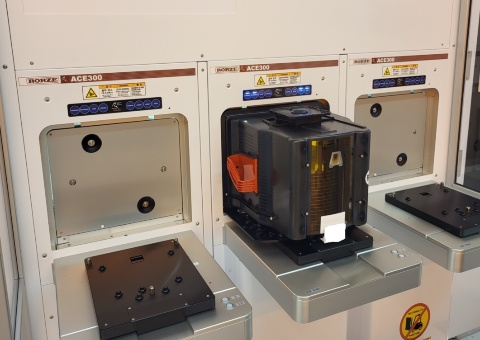
Stabilization of uptime through maintenance and troubleshooting on the process modules. This, in turn, contributes to production reliability.
For my daily work you need a basic understanding and good knowledge of the underlying mechanics, mechatronics, pneumatics, IT, and electronics. The job is extremely varied and wide-ranging so you learn something new every day.
I support different groups of ASH (“ashing”) modules so it is important to understand the specifics of each production machine and the differences between them.
As a woman, the chance to work in a largely technology-driven environment with a future-focused company.
My work is really varied and exciting. I try to bring a high degree of automation possible to our production lines in order to make the daily lives of my colleagues working in production as easy as possible.
Oliver's Story
Playing detective
Since 2018, Oliver has been a Maintenance Technician for Infineon Regensburg. His main focus is on the maintenance and repair of automation equipment. Because this entails interfacing with various experts, team spirit and staying power are key skills in his work.
Oliver in five words:
SportsEnthusiast Pioneer TechGeek SolutionFinder Optimizer/ImproverFor me personally, it is the combination of diversity in my work, close collaboration with my team, and the opportunity to develop myself and my skills. I can bring my strengths to the table and embrace responsibility.
Troubleshooting and maintenance of automation equipment.
Outside of office hours, I am the first port of call for automation questions, also interfacing between system experts, line experts, and shift supervisors.
In my short video I give an insight into my daily work.
I like playing the detective and combing through old documents to find the answer to a given problem. Every day brings its own little moments of success and these grow as you gain more experience on the job. Engaging with new technologies is also very exciting – say when a new machine is installed on the production line and we are there to experience the deployment live.
Working in a cleanroom is like stepping into another world. Intricate tasks like changing a screw are far from easy when you are wearing gloves. You need to have really good fine motor skills and to be generally fit. In addition to regular climbing feats and working on the machines in cramped postures, you end up walking a good 15,000 steps on an average shift.
Smart working. I always have my cleanroom bag with me – packed, for example, with common spares to replace parts subject to wear and tear. That saves me a lot of footwork. I also have an overview of all systems on my laptop so can prioritize trouble reports.
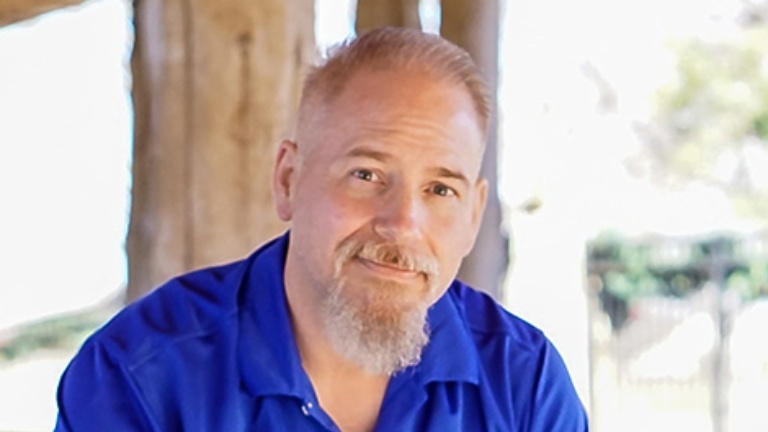
My position as an Equipment Shift Manager is very dynamic. I get to work with equipment engineers, production operators, and maintenance technicians every day. Being part of such a diversified team is a dream come true.
Scotty's Story
Challenging excellence daily
Having started out as a maintenance contractor in Austin, Texas, Scott (Scotty) became a full-time Infineon employee after 5 months in 2020. Equipment Shift Manager since August 2022, he facilitates the success of the maintenance team in the first half of the night shift by removing obstacles and challenging excellence daily. He is tenacious but compassionate.
Scotty in five words:
CoffeeAddict StrategicThinker Communicator TattooAddict ImplementerInfineon is the only company that I have worked with rather than for. I look forward to coming in every day to help others and make a difference. Infineon is like a second home for me.
My main tasks are to remove obstacles and enable the technicians on the floor to be successful in all their activities. Working with engineering, operations, and production staff to reach our shift and weekly goals is a critical part of my responsibilities. Listening, learning, and growing is a daily task that I value highly.
Being part of the success of my team and an effective manager and leader; earning the trust of my crew.
I am challenged daily to learn more, take on new and exciting tasks, and lead my team. My position is constantly evolving, and this keeps me on my toes.
I hold myself and my team to very high standards, sometimes a little too high. This is also a learning experience for all of us.
I started Infineon as a contractor, working as a senior technician in etch. After 5 months, I was offered a full-time position and promotion within etch. For another 1.5 years, I gained mastery of my module and was working in 2 other functional areas as well (implant/thin films). Just before my 2-year mark, I applied for the position of Equipment Shift Manager, did the interview and was offered the job. I work with the greatest team anyone could ask for. I am very proud of this achievement and cannot wait for the next step in my career with Infineon Technologies.
Previous story
Next story
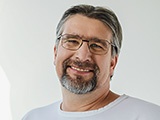
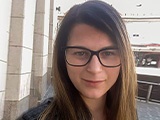
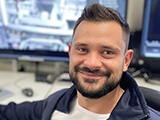
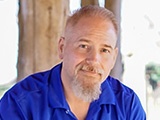