iMOTION™ Motion Control Engine (MCE) iMOTION™ MCE - Overview
All iMOTION™ products include a Motion Control Engine (MCE), which eliminates software coding from the motor control algorithm development process. As the core of all iMOTION™ products, the MCE speeds up the customer development time with its integrated ready-2-use motor control algorithm and production grade software. The MCE implements Field Oriented Control (FOC) and uses space vector PWM with sinusoidal signals to achieve highest energy efficiency.
The integrated state machine handler including fault states and multiple protections like over- and under-voltage, over current and rotor lock helps to safeguard motor and power stage. The MCE can control the motor running either sensorless or with sensor support like analog or digital hall sensors and is available with ready-to-use algorithms for boost PFC implementations. To meet a wide range of applications it is highly configurable and its scripting engine that executes customer scripts with access to the MCE, GPIOs analog inputs and a configurable UART grants flexibility for different applications. The MCE and thereby all iMOTION™ devices can be used in applications requiring functional safety according to UL/IEC 60730 (‘class B’). Powerful tools like the iMOTION™ Solution Designer reduce the implementation effort for a variable speed drive to a simple configuration of the MCE for the respective motor.
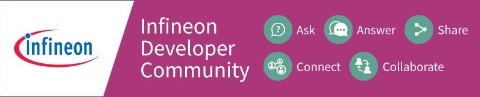
Our Developer Community is available 24x7 for you to connect and network with engineers across the globe. Get help from our support engineers, and expert members to solve your design challenges anytime, from anywhere, in any topic, and in your preferred language.
Control algorithm features
Motor control |
|
Special features |
|
Current and position sensing
Current sensing features |
|
Rotor position sensing |
- Two or three digital hall switches supported - Two analog hall elements supported
|
Protection
Integrated protection functions - Motor | Motor | |
Critical over voltage | activates zero vector breaking | x |
Flux PLL out of control | PLL not locked to rotor angle, maskable | x |
Over temperature | uses an external NTC | x |
Rotor lock | activate from min to 25% of rated speed, configurable detection time | x |
Execution | CPU load exceeding 95% | x |
Phase loss | motor phase disconnected or winding short, PARKING state | x |
Link break protection | UART communication lost | x |
Hall invalid protection | invalid hall pattern detected | x |
Hall timeout protection | missing hall transition, rotor lock, configurable detection time | x |
Integrated protection functions - PFC | PFC | |
AC over voltage | configurable threshold | x |
AC under voltage | configurable threshold | x |
Frequency fault | AC input frequency out of range | x |
DC-bus Open Loop | Missing or faulty DC-bus voltage measurement | x |
Integrated protection functions - Motor and PFC | Motor | PFC | |
---|---|---|---|
Over current/ gate kill | measured via shunt or as input from gate driver/ external source | x | x |
DC over voltage | configurable threshold | x | x |
Parameter load | configurable threshold | x | x |
DC under volatage | faulty parameter block | x | x |
Current offset calibration | checked after startup offset self-calibration | x | x |
Script engine
Scripting engine |
|
Features and functions |
|
Find out what iMOTION™ Solution Designer offers you, how projects are created and the work flow in terms of configuration, tuning, dashboards and scripting. The tool guides you through the complete project workflow, achieving the shortest time to market with the lowest R&D efforts.
State of the art sensorless algorithm for permanent magnet motor control is described in this video. Common pitfalls of sensorless control, such as a non-controlled startup are easily avoided with the Motion Control Engine (MCE) inside infineon iMOTION devices. A clean startup, without vibrations and oscillations is demonstrated with a low inertia fan motor.
iMOTION™ ICs integrate hardware and software functionality required for controlling PMSM motors with field-oriented control (FOC) (with and without sensors). iMOTION™ products are based on Infineon’s patented, field-tested Motion Control Engine (MCE), which eliminates software coding from the development process. As a result, all users have to do to implement a variable speed drive is configure the MCE for the respective motor drive system.
Discover how Infineon’s Modular Application Design Kit, or MADK evaluation platform, covers 3-phase motor drive applications with a power level that goes from 20 Watt up to 10 kilowatt.